The world’s most modern forest machine factory

Ponsse Plc’s production is located in Vieremä, in the Northern Savonia region. The current factory buildings have been built around the 300 square metre facility that was built by the municipality of Vieremä for machine entrepreneur Einari Vidgrén in 1970. This is not only where the factory began, but also the Ponsse spirit. Today, the factory has a total of four hectares of floor space.
In autumn 2018, Ponsse commissioned a factory expansion that comprised 1.3 hectares of new production facilities. The expansion is the single largest investment in the company’s history. The new facilities mean increasingly smooth and flexible production operations, and better productivity. Employees have usually enjoyed long careers at Ponsse. This is why the factory expansion also focused extensively on the well-being and safety of Ponsse’s employees, as well as on workstation ergonomics.
Above all, the new factory stands for better quality. Production is based on the idea that no compromises are ever made over quality. The amount of testing and quality control increased significantly in the new production process. Every production line ends in testing, ensuring that all manufactured structures are tested before moving on to the main line. The main line also ends in testing, when the engine and hydraulics are tested in a soundproof test room. Finished machines are transported on lowbed trucks to test logging sites where they undergo final testing in their real operating environment before they are delivered to customers.
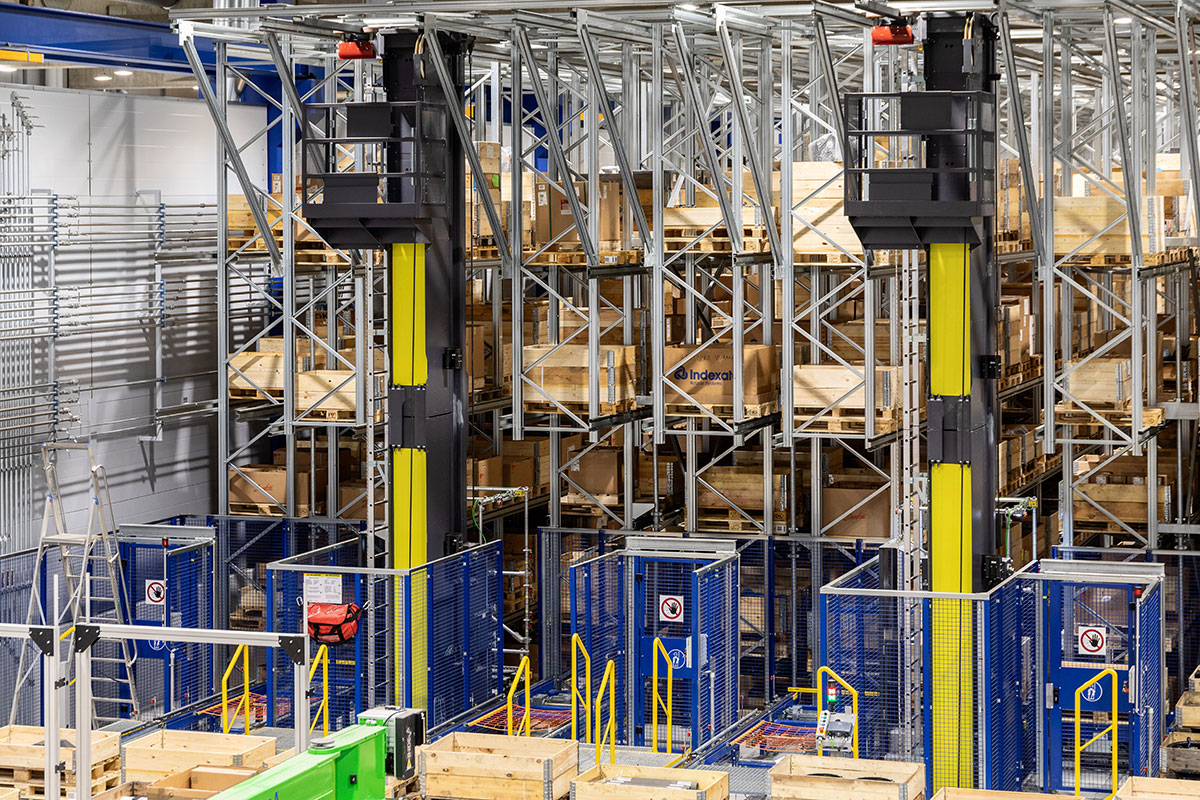
The particular production characteristics and extensive customer-specific variation of products also require a lot of power and accuracy from material logistics. The internal logistics operations were totally reformed in connection with the factory expansion and are now based on pull control. Warehouse automation covers 15,500 storage slots for small items and components, as well as 3,900 pallet positions. Along the assembly line, the parts and components required are picked automatically from the warehouse and transported to each workstation using automated guided vehicles.
The factory represents the latest technological solutions, also in its building systems. The new facilities focus particularly on energy efficiency. There is a solar power station on the roof of the factory with 640 solar panels covering an area of 2,000 square metres. The system has a capacity of 192 kWp, which is equivalent to the annual electricity needs of 100 homes. The factory is well lit with energy-efficient LED lights. In addition, regenerative braking systems are used in storage automation. The trolley system in the assembly line transfers machines from one work stage to the next, while the movement of the trolleys are monitored in real time.
The factory roof also produces energy savings, as the Noxite roofing material, together with sunlight, wind and rainwater, neutralizes hazardous nitrogen oxides caused by traffic and industrial operations. It also reduces the need for cooling during the summer.